InsigH2t will acquire the fundamental scientific understanding of the effect of pressure on the turbulent burning rate, thermoacoustic response, and emissions performance of lean premixed hydrogen flames under gas turbine relevant conditions. It will pursue experiments, and direct numerical simulations of canonical flame configurations over a range of elevated pressures to extract scaling laws, develop new combustion models for numerical simulations, and low order tools that will be applied to different industrial geometries of two OEMs. To do this a systematic experimental, numerical, and modelling approach will be adopted to deliver on the objectives. The overall methodology of InsigH2t is graphically depicted in the following picture, where the main project outcomes are highlighted:
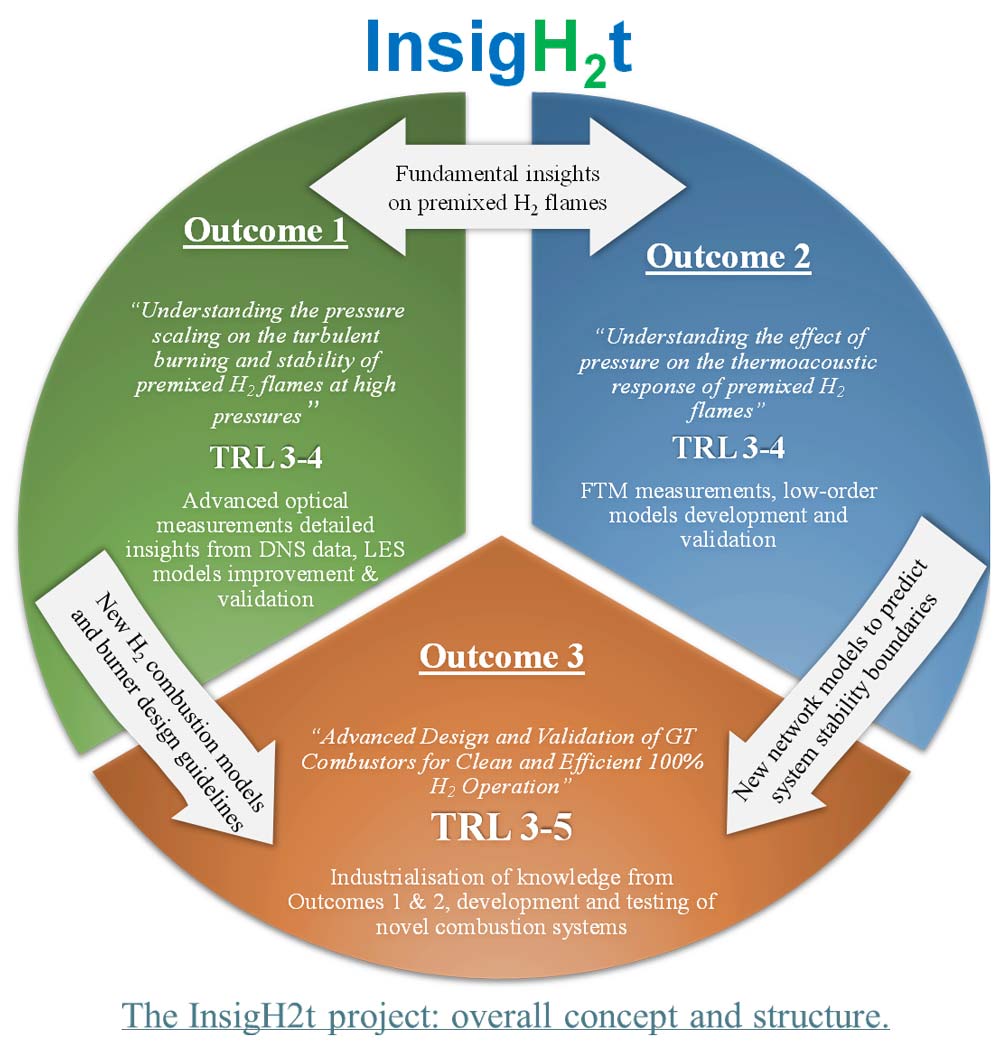
High pressure experiments
Two new high-pressure test rigs with unique capabilities to study fundamental flames at elevated pressures will be the main focus of the experimental research effort in Outcomes 1 and 2. The experimental work related to Outcome 1 will be conducted in a new high pressure, staged combustion facility currently being established at NTNU. The facility can operate as a single stage combustion facility to study the canonical premixed jet and swirl in propagation mode or in a sequential staged mode where the flame in the second stage is stabilised by autoignition over a backward facing step. The facility is modular to accommodate different burner geometries, grids/perforated plates to control the inlet turbulence, and has full optical access to the first and second stages for laser diagnostics. The focus of the research to measure the flame surface area and can accommodate different burner geometries and turbulence grids. Various laser based and optical diagnostics, such as low and high-speed OH-PLIF systems and PIV will be used.
A highly advanced high pressure test rig at TUB will be used to measure and characterise the thermoacoustic response of the canonical premixed jet and swirl flames for outcome 2. It has the unique capability of being able to test the flame dynamic response to acoustic actuation under GT relevant conditions. Upstream and downstream sirens are utilized for acoustic forcing. The acoustic field upstream and downstream of the burner is measured with an array of microphones to extract flame transfer matrices (FTMs). Exhaust emissions such as NOx will be measured.
Optical Laser Diagnostic Methods
Accurate experimental characterisation of the turbulent burning velocity is fundamentally challenging at elevated pressures. In premixed flames, the main approach is to acquire the highest possible resolution images of the flame front using planar laser induced fluorescence (PLIF) techniques to evaluate the flame surface area (FSA) which is directly correlated to the absolute turbulent burning rate.
Flame Transfer Matrix Measurements (FTM)
The FTM describes the relationship between the acoustic velocities and pressures upstream and downstream of a flame. From a control-theory perspective, it treats the dynamic flame response as a 2-input 2-output element. To measure an FTM, specialized equipment that can introduce controlled acoustic perturbations to the combustion system and measure the resulting responses is required. This includes (i) loudspeakers or siren drivers, to introduce frequency-dependent acoustic perturbations; (ii) two arrays of microphones, to measure the acoustic pressure at various positions both upstream and downstream of the flame.
Chemiluminescence measurements
To measure the mean flame shapes and dynamics for different operating conditions (pressures, temperatures and equivalence ratios) OH* chemiluminescence (308 nm) will be measured using several methods: (i) photomultipliers, which provide time-resolved, spatially integrated OH* intensity, and (ii) high and low speed intensified cameras equipped with OH* filters, which record the 2D spatially resolved (line-of-sight integrated) OH* intensity. These methods will be used extensively in Outcomes 1 and 2 as an essential measurement tool for flame characterisation.
Direct Numerical Simulation (DNS)
DNS predicts turbulent combustion processes based on a first-principles approach in which high-resolution simulations directly solve all elementary chemical reactions that take place in the flame and all time and length scales of the turbulent reactive flow. As such, DNS provides the most accurate numerical solution of turbulent combustion processes with the widest possible data completeness. Accordingly, DNS represent an optimal tool to obtain accurate estimates of the turbulent burning rate that characterises turbulent premixed hydrogen-air flames at high pressure.
The DNS can play an important role in the development and validation of data processing methods that can be then applied to experimental data obtained from advanced optical measurements to provide more detail into of the effect of pressure, turbulence and preferential diffusion on the local flame structure and global burning rate. In this work the DNS will also help develop data processing methods from the high-pressure experiments for the robust extraction of the turbulent burning rate.
Large Eddy Simulation (LES)
Highly resolved LES modelling will also be adopted to analyse flame wall interaction at burner lip where ‘edge’ flames are expected to act as the anchoring flame elements. Conjugate heat transfer will be employed to properly account for flame heat losses. The objective is to understand the mechanisms of flame anchoring/quenching and deduce a dedicated phenomenological model to be used in classical, lower-fidelity design-oriented LES investigations.
Network Modelling
It is common practice to represent the thermoacoustic behaviour of combustion systems by making use of network models. This approach is very powerful in simulating many different operation conditions due to its low computational cost as when compared to high-fidelity numerical simulations. Network models divide the thermoacoustic response of a combustion system into a set of modular subsystems, plenum, burner, e.g., flame, combustion chamber as shown in the following figure.
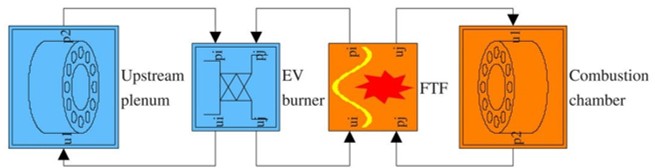
For the network model approach used in InsigH2t, FTFs/FTMs measured at different pressure conditions and analytical physics-based expressions are included in the network model for the combustion system to be simulated. In addition, the network model can be used to identify or optimise suitable countermeasures as for example acoustic dampers and burner staging. Passive acoustic dampers are typically installed within the combustion chamber to mitigate strong combustion dynamics.
Burner development
The combustion development process consists of several steps starting from an initial combustor conceptual design followed by the necessary considerations towards commercial deployment. The development process includes dedicated steps addressing air distribution optimisation, CFD modelling, cooling, and mechanical integrity evaluation of proposed concepts, thermoacoustics, operation concept, as well as full-scale atmospheric and high-pressure testing.